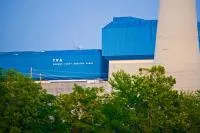
Flowserve helps resurrect browns ferry unit 1
For 17 years, Unit 1 at Browns Ferry nuclear plant on the north shore of Wheeler Reservoir in northern Alabama sat dormant. One of three operating Tennessee Valley Authority (TVA) nuclear plants, Browns Ferry is a three-unit GE design and began commercial operation in 1974, just 11 years before it was shut down in 1985. When the TVA decided in 2002 to return Browns Ferry Unit 1 to operational status, extensive decontamination, repair and replacement work were necessary to bring the unit up to present-day standards. The TVA chose Flowserve to help them tackle the unique challenges associated with bringing Unit 1 back online.
Radiation Hazards
High radiation levels required repairs and modifications to take place at an off-site facility. Workers transported equipment in secure containers with lead shielding to Westinghouse Electric Company’s Waltz Mill Nuclear Repair Center in Madison, Penn., where radiation was reduced to workable levels. It was also necessary to jockey large components in and out of storage multiple times due to space restrictions.
"This was a joint project between the Flow Control and Pump Divisions at Flowserve," says John Chappell, Flowserve Raleigh general manager. "We were reworking valves in the facility, while at the same time also doing some pump components."
Lead Times
The TVA’s ambitious schedule did not permit standard or even the typical expedited lead times. However, through extensive coordination with the foundry and Flowserve’s Raleigh, N.C., facility, Flowserve cut lead times down to just six weeks.
"For us, the biggest issue a lot of the time is raw material lead time—getting what we need from sub-suppliers," explains Chappell. "We spent a lot of man-hours working with suppliers to improve lead time." John Underwood, senior manager at TVA Browns Ferry Nuclear, saw Flowserve’s ability to deliver on time as an area where the company excelled. "Meeting [TVA’s] deadlines for installation of components helped make the project successful," he says.
Go with the Flow
Adapting to changing circumstances as the repairs were under way was also critical to Flowserve’s success. During the project, four of the 14 valves to be decontaminated were found to be beyond repair. Flowserve’s Flow Control and Pump Divisions manufactured the four new valves over the course of the next year. They also completed new bonnets for four of the 10 decontaminated valves as well as RWCU pump impellers. TVA ordered an additional 10 replacement valves for critical service inside the containment. "We think we did a really good job at Browns Ferry," says Chappell. "It was a pretty difficult project with a lot of difficult times, but when it was all done, TVA thanked us for sticking with it."
Electropolishing
Flowserve also gained its first nuclear experience with electropolishing, the electrochemical removal of microscopic irregularities from metal surfaces, which TVA required for all decontaminated and new valves, including bonnet and body parts, and the pump impellers ordered from Flowserve. Electropolishing minimized rough surfaces where radiated contamination might adhere, reducing hot spots in the system. The extra step will reduce radiation exposure for workers during future maintenance activities.
"Electropolishing was new for us in nuclear valve manufacturing," Chappell says. "We had to work things out not just from a schedule standpoint, but also physically figure out how we were going to do it. It makes for a beautiful product—really smooth and shiny. There is no place for radioactive byproducts to accumulate."
A Partnership
Flowserve Flow Control Division worked closely with the Pump Division to make the project a success. The Pump Division helped realize one objective of the project, which was to increase plant power output by about 20 percent. This increase in output required the replacement of the existing high-speed 8,500-horsepower reactor feed pumps originally supplied by a Flowserve heritage company. Flowserve worked with the TVA to develop a design that would not only allow the reuse of existing steam turbine drivers but would also minimize modifications to existing piping, resulting in significant cost savings. Flowserve manufactured the pumps in Spain and tested them at full power and speed in California.
"The pumps met and exceeded TVA’s specifications," says Fred Grondhuis, Flowserve Pump Division high energy and nuclear products marketing manager.
The Pump Division also worked with the TVA to replace the inner assemblies of the Flowserve reactor recirculation pumps with a patented upgrade called the Fourth Generation design. Total value of the work done at Unit 1 for the Flowserve Pump Division exceeded $15M.
"The ‘Fourth Gen’ is the definitive solution to thermal fatigue shaft cracking, which has been an industry-wide issue in this service," says Dave Mathewson, Flowserve Pump Division nuclear products director.
"By providing a turnkey change-out, Flowserve was able to control the installation and manage the project of replacing the reactor recirculation inner pump assemblies under budget and on schedule."
Browns Ferry Unit 1 was finally brought back online in 2007. Currently, Unit 1 provides 1,155 megawatts of power, and the TVA plans to eventually increase each unit’s capacity to 1,280 megawatts. The TVA is also in the middle of construction on Watts Bar Unit 2, which will add another 1,180 megawatts of power when completed.