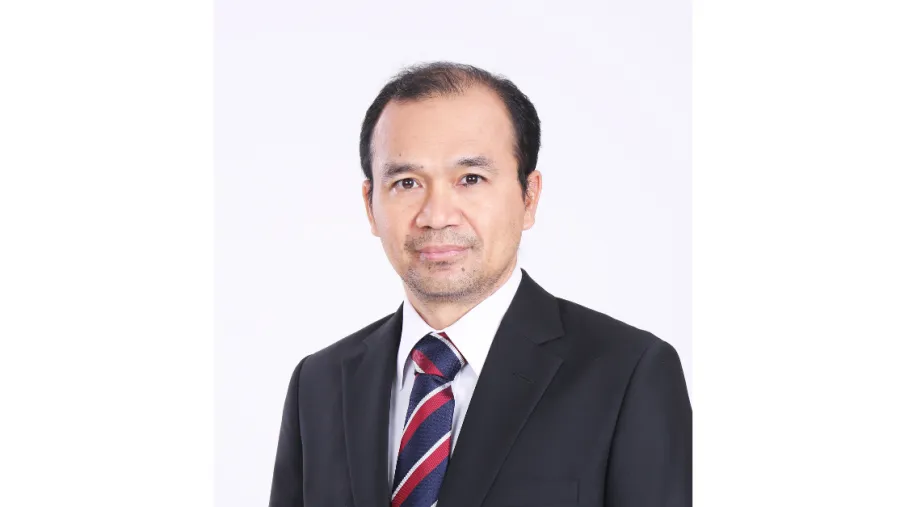
Facing The New Era of Power Management
As the winner of the Silver award for Geothermal Power Project of the Year, Information Technology Project of the Year in Indonesia and Power Plant Upgrade of the Year in Indonesia in the Asian Power Awards 2021, PT Indonesia Power is confident in facing the new era of power management.
PT Indonesia Power, a subsidiary of PT PLN is the largest power company in Indonesia operating various power plants in the coal, natural gas, diesel, hydroelectric, and geothermal sectors. Since 2015, the company has been managing their energy system with the 5E strategy—Enhancing, Embedding, Energy, Efficiency, Excellence.
Kamojang Power Generation and O&M Services Unit (POMU), with a total capacity of 375 MW, is one of the units of PT Indonesia Power and is used for Geothermal Power Generation in the country.,
M. Hanafi Nur Rifa'I, Director for Operations of PT Indonesia Power said that based on review analysis, turbines use 79% of energy which can go up to 92% due to operational problems especially those related to building up or scaling the energy. “This indicated that improved effectiveness in the turbine washing was required. For this, the company has designed the Geothermal Analysis Engineering Software (GAES) to perform smart and user-friendly analysis on geothermal turbines and help companies address existing problems as soon as possible.
“One of the main modules of GAES is its turbine analysis which uses steam flow rate constriction analysis method by nozzle blocking ratio, our NBR parameter,” Hanafi said. The module also can model the scale rate of the turbine and help predict the rate of derating.
“The positive result that can be achieved by using this software is increasing the efficiency of Kamojang from 89.84% to 95.08%, equivalent to derating prevention of 288 MWH with a financial benefit of more than IDR1b in a year,” he said. This can also decrease the greenhouse gas emission by 2284.5 tonnes of CO2 equivalent through saving steam consumption after turbine washing by 15.92 tonnes per hour.
Digitalization of power plants
In the new era, PT Indonesia Power aims to be the pioneer of the breakthrough digital power plants with the new system called Reliability and Efficiency Optimization Center (REOC). The digital system can be used by companies to remotely check on all their operations and maintenance parameters as well as optimise them in real-time to achieve reliability and efficiency.
Hanafi notes that using the REOC, companies can optimize the essential parameter of efficiency such as gas temperature and ensure that the essential parameter of reliability remains to prevent the force of energy. The digital power plant is the centre of REOC and they are ready to adopt the latest machine learning technology.
The digital power plant of the REOC has been categorized into four levels:
- Level 1: Remote monitoring of the system.
- Level 2: Optimization of the plant operation
- Level 3: Real-time predictive and prescriptive maintenance engineering operation using the Machine Learning technology.
- Level 4: Digital business solution using Artificial Intelligence by 2025.
During its development, PT Indonesia Power Digital Power Plant has been using data science and machine learning to perform real-time, predictive, and prescriptive maintenance, optimizing maintenance costs, and increasing reliability. “For example, we can predict the replacement period of the gas turbine air filter, the level of the risk of the boiler, the temperature, and several other parameters that are very important for reliability. Real-time predictive algorithm capabilities were also developed by our engineers with their expertise,” said Hanafi.
Managing the risks
Since 2012, PT Indonesia Power has established a risk management system for running the power industry business. Hanafi said that their principal process and framework of risk management were ready and were defined well by the company. He underlined that identifying and mitigating the project is one of the important factors in achieving the goals. “The identification of our risk in each aspect in our project which are administration, work procedure, testing, commissioning, etc. The fundamental risk is also health and safety,” Hanafi said.
Hanafi said that their project isn’t only targeted on its quality but also budget, time, the scope of work, safety, and also safety compliance. Zero accident and health is the prioritization work permits done digitally and health and safety environments monitored frequently by the HSE operation.
One key risk factor of the project is also the cleaning process to make sure the steam quality meets the requirement of the operation. This process takes a lot of time and the company functions as an environmentally friendly power plant to motivate the company to ensure the people who live near our power plant are not being affected by any of its processes. “Proper scheduling and well-controlled operation help achieve that condition,” Hanafi said.
Hanafi underlined the three main factors that make execution well are (1) the human capital and its culture knowledge base and multi discipline competencies, (2) development of detailed missional project management process, also target scope and critical parts are maintained to ensure that the project is executed in excellence manner. (3) integrated regular performance monitoring starting from the executor level to the director. The decision will be made quickly and precisely. All of this makes the execution of the PT Indonesia Power project plant well in quality and time.