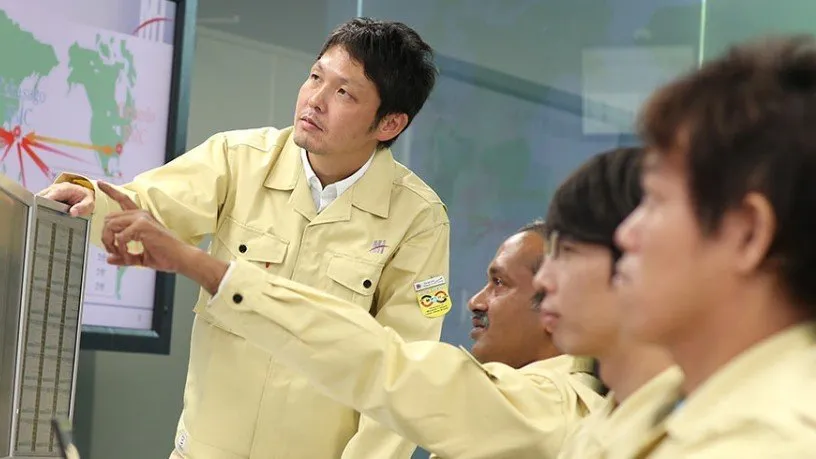
Powering up on maintenance to optimise power plants
After-sales and maintenance services are crucial for power plant optimisation
Asian Power spoke to Ziad Khalaf, Senior Vice President, Operations for Mitsubishi Power Asia Pacific for insights into how after-sales and maintenance services benefit power plant operators
How have after-sales and maintenance services evolved over the years?
For the services and power plant sectors, we need to keep up with advancements in technology. When you install something for the first time, there is a learning process which involves a collaborative effort between equipment manufacturers and operators to identify problems and find solutions. We leverage our extensive experience to find these solutions efficiently, and any learnings end up being shared within the industry.
The equipment manufacturer has the main responsibility to evolve and develop improved solutions for the equipment. For example, gas turbines used to be maintained following a certain number of operating hours. Over time, we develop enough operating experience and knowledge of the behaviour of the machine and can stretch the maintenance cycle which reduces the downtime of the equipment. This saves money and avoids unnecessary maintenance.
How has Mitsubishi Power powered deep innovation in after-sales and maintenance service?
Technology advancements allow us to maintain power plants faster and cheaper through solutions such as robotic inspections of generators. Rather than having to disassemble the generator and spend a month crawling around in it, inspecting it, and risk causing damage, we use robots. These are little measuring instruments that can go into the generator, crawl on their own, and do the inspection. This can be done in three to four days, which saves a lot of money and avoids a month-long disassembly. We've done robotic inspections in Singapore and other parts of the world.
What stands out about your after-sales and maintenance service in Asia?
We are a leading service provider with a strong presence and commitment in Asia. In the Philippines, we have capabilities that service the region and provide services to other parts of the world. This includes remote monitoring of power plants, advanced technologies of data collection, analytics and artificial intelligence. It's a self-learning system that monitors the power plant and gives feedback on how to improve the operation maintenance in the plant. It is therefore a system that learns, evolves, and provides additional information to the power station.
Mitsubishi Power’s TOMONI HUB helps make power plants more reliable and profitable
Do you have data-based solutions?
We have TOMONIₜₘ, which is a package of different modules that leverage remote monitoring, advanced digital control systems, predictive analytics, and AI to optimise plants. We collect the data from the plant, monitor it remotely, analyse it; and then we provide customers with different services that come out of this data collection and analysis process. It helps plants operate more reliably and achieve efficiency improvements. To execute this, we have a global network of TOMONI HUBs with these services, including one in Alabang, Philippines.
How can a power plant operator justify the costs of after-sales services to their stakeholders?
The biggest cost in operating a power plant is the fuel consumed. Previously, in a plant I managed, about 80% of the cost of operating it came from the fuel. So even if you take 50% to 60% of the operating cost of a plant which is fuel cost, and you can save 1% or 2% of that fuel you're consuming, that is a lot of money. It will also lead to a significant reduction in CO₂ emissions. When you do good service planning and execution, you can save money by improving efficiency. You're saving on fuel consumption, saving money, and still producing the same energy that you're expected to sell. Less fuel burned also means reduced emissions.
The maintenance, it's always tied to the economics of the power plant and compliance with regulations and policies.
How do you help power plants in the region improve reliability?
Reliability of a power plant means that the plant can keep running well and not unexpectedly shut down and be forced to stay down. We recommend for our customers to have good operating maintenance practices to improve and keep their plant reliability high. If we have a new product learning from our experience in a power plant somewhere in the world, we issue bulletins to all our customers worldwide to inform them of key updates.
We also have a global users group meeting that provides members with an opportunity to learn about new improvements or changes to improve reliability. We're learning from each other and sharing information. Customers may be sharing information with one another. But if they send it back to us, we have access to all of these plant operators. When someone raises an issue about a problem in their plant and there is no solution for it yet, we take it on and solve it, and share the solution. That helps improve the reliability of power plants.
Technology and skills transfer are critical to power plant optimisation
How does Mitsubishi Power encourage technology and skills transfer?
Skills transfer is happening at different levels of the business. A power plant operator that has our equipment needs to know how to operate it. We work with our customers to teach them and train their operators on how to operate the plant through the construction, warranty and troubleshooting phases. The customer may assign their operators to work with our technical experts across the lifecycle of the plant.
We also offer training opportunities, and it's up to the customer to decide what they need. It's a combination of technology transfer and the development of skills amongst people.
In the Philippines, we have training centres with hundreds of engineers and people with different skill sets working in our facilities. They're all learning the technology. In Indonesia, we are hiring and training local engineers to become technical advisors to support the local market. We have a large installed base in Indonesia and manufacturing facilities in the Philippines. We invest a lot in local manpower in these countries to help them become skilled at solving problems. That includes technology transfer such as teaching new technical skills.
We also do a lot of research. In Indonesia, we work with PLN Group and the Institute of Technology in Bandung, Indonesia, to conduct feasibility studies and research on alternative energy technology and uses.
How can you support the energy transition?
Mitsubishi Power is helping to develop solutions for the energy transition. One major clean fuel that the company is focusing on to help customers transition to net-zero emissions is hydrogen. Emissions from producing hydrogen can vary, with green hydrogen-producing zero missions. Hence, we are advancing our natural gas turbine technology to co-fire with hydrogen, which will lower the overall emissions of gas-fired plants. For example, we are increasing the ratio of hydrogen co-firing into gas turbines – our J-series gas turbines are already capable of operating on a gas and hydrogen mix of 70% and 30% respectively, which helps reduce around 10% of CO₂ emissions. We have plans that by 2025, hydrogen firing will reach 100% commercially.
Mitsubishi Power supports the region’s transition towards cleaner energy sources
Can you talk about your regional presence?
We've been in the region for more than 50 years, providing equipment which ensures the stable, reliable and efficient supply of energy to countries around the Asia Pacific.
We have taken significant steps and increased our local support network — hiring people in each country to be closer to our customers. We stand by our equipment and spend a lot of effort in our production and research facilities to improve existing technologies or develop new technologies to improve plant performance.
We know what our customers need – efficiency, availability and reliability are important. They also have to save costs and produce as much energy as possible to meet demand. With time, there will be new needs for these power plants, whether it's additional environmental enforcement or the impact of upcoming climate agreements. We can provide solutions to keep the plants running while reducing emissions — you don't have to tear them down to put in something new. For example, you can clean up the gas coming out of the plant to comply with standards. All of that can fall into the service side of things. Also, we are a major player in new technology solutions. So, as power plants transition to more advanced technologies, whether it's renewable or hydrogen-based, we can help.
In Indonesia, we're planning to help customers integrate biomass burning into their thermal plants. There is a limit to how much you can do without changing anything in the power plant. Later, if you want to introduce more biomass or other clean fuels such as ammonia, you might need to make modifications. This falls into after-sales services. So you have the immediate needs of reliable operation and efficient operation and the future needs, which is the energy transition that Mitsubishi Power can support.