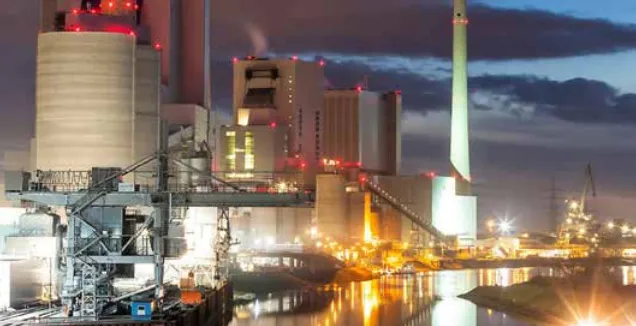
Hilliard Corporation: Keeping turbomachines in shape through HILCO's top-notch filtration systems
HILCO’s filtration products and services engage dry resin ionic exchange and keep power plants in shape.
When engineers first examined the power plant which provides electricity to the historic Texas A&M University, they discovered an alarmingly high level of varnish formation. Realising that uncontrolled varnish formation can wreak havoc on the university’s power supply, Texas A&M Utilities and Energy Services immediately contacted Hilliard Corporation to solve the problem.
Using its patented dry-resin ion exchange cartridge in the oil conditioning system, HILCO was able to drastically reduce the varnish in the lube oil in a span of three short months.
“Acid and varnish have been a problem for a number of years basically due to the number 2 base stock oils that power plants are using now. Over the years, they’ve become a problem due to the acid becoming a varnish, which coats critical components such as control valves and interior portions of reservoirs,” explains William Cantando, sales manager at Hilliard Corporation.
Varnish formation is the nemesis of hydraulic systems. Varnish formation is caused by the buildup of insoluble contaminants which are too small to be trapped by many commercial filters, coating hydraulic valves and pumps.
These contaminants are prevalent in the base oil stocks which many power plants use, making power plants particularly vulnerable to this insidious process. The increased friction created by varnish buildup results in equipment damage due to increased wear and tear, as well as less fuel efficiency due to shorter fluid life.
This is why an efficient filtration system is crucial to ensure that a power plant remains in tip-top shape. Varnish formation is a serious problem that degrades power plant operations, and can lead to massive losses if left unchecked. Thankfully, HILCO’s top-of-the line filtration systems can easily bring fluid contamination problems under control.
HILCO solves the problem of acid and varnish buildup through its patented dry resin ion exchange technology. The severity of varnish formation can be aggravated by specific oil chemistry, hot spots in the lube oil system, and static discharge. HILCO’s ionic exchange technology has proven to be an effective method in reducing varnish potential in a wide variety of applications in both mineral and synthetic fluids.
“We’ve come up with a patent technology called dry resin ion exchange. That particular product has become an industry leader in removal of acid and varnish in a system. It uses dry resin beads that absorb the acid and the varnish in the system and aggressively removes it,” Cantando says.
Patented technology
The patented dry resin technology absorbs varnish and acids but does not add dust or migrate into the fluid. The dry resin can reduce a fluid’s total acid number using as little as 0.01 pounds of resin per gallon of fluid.
This makes it a cost-effective treatment method that offers a value for money which is truly hard to match. “The dry resin ion exchange uses an hourglass-designed cartridge that eliminates exposure or blowing up that we see in other systems,” adds Gregory Bickham, regional sales managers at Hilliard Corporation. “Using this technology, there is no particle distribution downstream, so it eliminates the need for a trap filter downstream,” he explains.
HILCO brings fluid contamination problems under control, cost effectively with our full range of engineered filters, cartridges, reclaimers, coolant recyclers & fluid conditioning systems. But HILCO offers far more than just filters. It provides a full service fluid management process, from obtaining samples, to fluid analysis, consulting on equipment, field techs, start up help, and more.
HILCO also offers ionic exchange cartridges, designed especially for reducing total acid number levels in phosphate ester based hydraulic systems. The ionic exchange cartridges are also an efficient remedy against varnish formation.
The severity of the varnish formation can be aggravated by the specific oil chemistry, hot spots in the lube oil system, and static discharge. HILCO’s ionic exchange technology has proven to be an effective method in reducing varnish potential in a wide variety of applications both in mineral and synthetic fluids.
Fighting off static discharge
Another problem plaguing turbomachines is static discharge. This phenomenon occurs when oil generates sufficient static electricity to form sparks. This form of oil degradation has been studied extensively in many systems, including large frame gas turbines.
To remedy this, HILCO also offers an antistatic cartridge which features conductive fibres which are co-pleated in between two layers of hi-performance microglass filter media. This cartridge is used to address the extremely low fluid conductivity of Type II lubricant base stocks used in turbo machines.
“The problem with base II stock oils is the conductivity of the oil. So what this cartridge actually does is it lowers the conductivity of the oil and eliminates the static discharge seen in the systems,” Bickham says.
As a result, static charges can build on the nonconductive components of the lube oil system, such as the filter. When a sufficient charge is accumulated, static discharge occurs. Over time, static discharge contributes to troubling oil degradation and varnish buildup.
But with the anti-static filter, the static charge build-up can be dissipated before discharge can occur. “The anti-static cartridge eliminates the static discharge in the system, which creates the varnish. We use a product that actually has different parts in it, non-conductive parts, so that the static discharge is not permissible inside of the system,” Cantando adds.
Originally developed in the 1990s to solve a static discharge problem for a power plant in Japan, HILCO’s customers have successfully relied on the anti-static filter element for years. The anti-static charge elements are offered as a direct replacement for all HILCO standard size filter elements.
In order to determine fluid conductivity, HILCO offers full laboratory services and can verify the conductivity of a user’s oil if a static discharge problem is suspected. The reliability and efficiency of any filtration system are chiefly dependent on the quality of the cartridges used in it. HILCO has a full line of filter cartridges for virtually every application depending on size, filtration efficiencies and dirt-holding capacity.
Most fluids can be restored to an almost brand-new condition. HILCO’s on-site testing facility is continuously examining and improving cartridge performance as customer’s needs evolve. HILCO is a major to the supplier to original equipment manufacturers worldwide.
HILCO is part of the Hilliard Corporation, a world leader in motion control and filtration products since 1905. For over a century, Hilliard has been engineering, manufacturing and distributing motion control and filtration products. Its extensive history, expert knowledge of applications and strict quality standards makes the company a leading industry supplier.
A century of expertise
Hilliard’s large portfolio of products can be modified to meet new applications. Hilliard is an ISO 9001:2015 certified organisation.
“The HILCO Corporation has been in business for over a hundred years. We have our own R&D lab as many companies do. However, being an OEM favourite, we see more of the problems in the field than many other companies do. We’re an engineering-based type company, so it gives us the ability firsthand to look at an issue or a problem and try to solve it immediately many times before our competitors do,” Cantando says.
With a sound understanding of engines and filtration devices, Hilliard engineers design complete systems, including electromechanical interfaces. Hilliard often works with customers to research and test products, acting as a lab for specific applications.
Each of its processes is documented to regulate operation, even on very short production runs. Experienced machinists and code welders work efficiently to keep operating costs low whilst transforming blueprints into products.
Following documented processes, these craftsmen use bar-coded, computerised production controls to guarantee high-quality output. The company’s goal is to manufacture products that solve customer problems. And over the years, it has found that the only way to reach that goal is to be flexible. This is why Hilliard is willing to modify existing products, or develop new ones, respond quickly to requests, and take on complicated projects for other highly sophisticated applications.