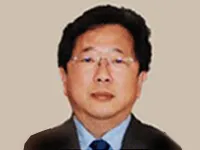
Here’s why most companies are reducing their energy cost
By Henry LauToday, we are witnessing a potent combination of factors, which together are driving organizations across the process industries to optimize their energy consumption. In the oil refining, petrochemical and gas processing businesses, in particular, energy is one of the largest components of operating expense. Limits on nitrogen oxide and sulphur oxide, regulations to control ‘flaring’, and restrictions on greenhouse gas emissions are combining to push the issue up the business agenda.
This trend is further strengthened by the ongoing global economic downturn, which is seeing industry delaying large investment projects and focusing on cost reduction and stay-in business initiatives. Improving energy efficiency saves costs with no negative impact and therefore represents a particularly attractive option for businesses to follow at this time, especially given that in the near future many companies will also be faced with having to buy CO2 emissions credits. Being more energy efficient therefore has a double impact on the bottom line – it reduces both operating expenses, and expenditure on CO2 credits.
So today, reducing energy costs is on the agenda of most companies in the process industries. One of the key issues that they are facing, however, is that there are many different ways to reduce energy cost. Consequently, in developing the most appropriate energy improvement strategy, organisations need to consider all of these different options.
Role of the United Nations
With the United Nations COP15 conference held in Copenhagen in 2009, interest has been growing in the role of Carbon Capture and Storage (CCS) in driving the reduction of CO2 emissions for energy intensive businesses. The need to cut environmental emissions is certainly urgent. The International Energy Agency (IEA) predicts that by 2030 demand for energy will increase by 50% compared to today. The increased demand will drive up carbon dioxide emissions and heighten the climate change problem, making the efficient use of energy key to resource conservation.
It is true that CCS has great potential as a method of addressing these issues. This is underlined by the fact that leading companies in the energy sectors are engaged in piloting programmes using technology solutions.
One of the key challenges in CCS is carbon capture and many leading companies are using process modeling solution for carbon capture modeling to find ways to make carbon capture viable and cost effective solution in shortest amount of time. However, the pilot programmes are in early stages and it will take time for these programmes to demonstrate commercial viability in meeting the carbon capture challenges. This, together, with the fact that the long-term effects of storing large amounts of CO2 underground is unknown, means that widespread adoption is unlikely for the foreseeable future. While businesses explore the CCS potential, there is much that heavy industry sectors, such as oil and gas, and chemicals, can do to sustainably and cost-effectively reduce carbon emissions through the more traditional practice of efficient energy management in their plants and assets.
Scoping the Challenge
In a high-level report delivered by Tony Blair before the Copenhagen conference, the overall global requirement to reduce energy emissions is daunting.
According to “Breaking the Climate Deadlock, Technology for a Low Carbon Future” a recent report produced by The Climate Group and The Office of Tony Blair, ”to put ourselves on a path to meet our emissions goals, we need to reduce global emissions by 19 Gigatonnes (Gt) in 2020 and energy-related emissions by 48Gt by 2050." In meeting these targets the potential offered by enhanced energy efficiency across industry alone is significant. The paper indicates that approximately 19% of total savings in energy related emissions to 2050 could come from industry.
With the scale of the problem and industry’s contribution defined - together with the current discussions in Copenhagen centered on further reduction proposals with specific timescales - it makes sound business sense for industries to optimize their energy consumption. Heavy industry organizations, in particular, can reduce operational expenses, drive bottom-line improvements and improve business performance. After all, for many of these businesses, energy costs represent the second largest drain on budgetary resources after raw materials.
This is particularly pertinent in the current economic climate. As profitability levels fall away, there is less money available for capital projects. Businesses will want to push assets to energy efficiency limits in order to reduce operating costs before considering investment – so they will need to focus on ensuring optimal energy performance.
Of course, the way in which organizations interpret energy management varies. Typically, the key challenge will be to identify the combination of improvements that best meets the demands of the existing production processes and utility systems and maximizes potential in line with business objectives.
An integrated and holistic approach to energy performance management can achieve significant savings in energy costs and hence greenhouse gas emissions both within the manufacturing units and in the utilities systems that support the manufacturing units.
An important component of the solution is provided by model-based energy management systems such as those produced by AspenTech, which can be used to help take advantage of potential savings which have hitherto been largely unexploited in addition to providing optimized and consistent information about a site’s key processes and facilities for decision-makers.
This knowledge can be useful both in long-term, strategic decisions and in concluding energy supply contracts, in preparing budgets and in drawing up investment plans, as well as in optimizing the energy costs of ongoing operations – based on current demand, costs and plant availability.
Sustainable Benefits
The potential benefits to businesses of this kind of holistic approach to energy management are huge. Adopting best practice here can have a major bottom-line benefit since savings of between 5-10% can be obtained using operations planning and optimization without needing to make any significant capital investment even in the most sophisticated plants.
By implementing an energy management program with elements focusing on both supply and demand, organizations can achieve significant returns - often over 15% of their annual energy costs with very attractive payback on the capital invested. So the best practice is to develop a sustainable approach, involving the continuous monitoring of operations and focusing on making improvements to the implementation.
For organizations operating in this sector, the ability to see how they are doing against a plan, a contract or a budget is all part of being able to improve the energy side of the business. As energy becomes a constant metric for operational performance for the organization, users will begin to see sustainable and continuous process.
Henry Lau, Senior Vice-President and Managing Director, Regional Sales and Services, AspenTech APAC