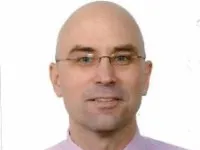
A comprehensive guide to energy management in process industries
By Rob BrendalMost companies in the process industries are working hard to reduce their energy consumption and the resulting emissions. But the benefits achieved through standalone, one-off projects can be lost over time.
In order to be effective in the long run, a comprehensive program is necessary that addresses energy in all aspects of the business, and for each role within the organization. A holistic, consistent approach will help manufacturing sites to minimize energy consumption and maximize production efficiency.
Four activities for lifecycle energy management
Recently many issues have resulted in renewed interest in reducing energy consumption by industries in all areas of the world. These include concerns about CO2 emissions, cost reduction in the current financial slowdown, and energy security among others. One of the best ways to address all of these issues simultaneously is to improve the energy efficiency of existing operations.
The process industries are not exempt from these pressures. Many such sites have energy and emissions management programs in place or are preparing to implement them. Programs that are ad-hoc or limited in scope may produce positive results temporarily, but in order to achieve lasting, sustained improvements a comprehensive program with well-established goals is required.
An effective energy management program for manufacturers – that is, one that enables an organization to reduce energy consumption through systematic actions – is multifaceted in that it must involve many people and functions in an organization.
A comprehensive program that will have lasting positive effects on energy consumption for a complex site will do the following:
- Design the plant for efficiency
- Maintain the equipment for design performance
- Control the processes to reduce energy consumption
- Operate intelligently to keep efficiency high
As illustrated in Figure 1, these areas work together as pieces of an overall, comprehensive approach to energy.
Figure 1: An effective approach to energy management is comprehensive in scope.
Note that these activities involve different people within the organization, and they occur on different time frames. The design activities are generally done only during the initial engineering phase for a site, or during capital projects after the units have been put into service.
The maintenance activities are done periodically, often during plant shutdown periods but sometimes online during production for some equipment. The control and operations activities are on-going and continuous; achieving efficiency through these are addressed daily at the best-managed sites.
Shown below in Table 1 are examples of the types of activities engaged in for these four areas:
Table 1: Example areas of focus for an energy management program.
Energy management in the design phase
The ultimate energy efficiency of a process unit is to a large extent determined during the design phase. Choices made in this stage will have lasting effects through the life of the unit, and they typically constrain the maximum efficiency achievable once the units are in operation. These choices include selection of major equipment, inclusion of unit operations intended to recover low-grade waste heat, and even overall technology choices from licensors.
Evaluation of various options will consume time and budget in the design process; so among the most important steps during the design phase is to set aside resources such that energy efficiency is considered early in the process.
When energy is simply an add-on activity late in the design stage after most major decisions have been made, the only result is often a list of those changes that could have been beneficial, but that cannot be investigated without significant delays in the overall project schedule. These changes are almost never implemented, with the lost opportunity affecting the performance through the entire life of the process unit.
Energy management through maintenance
Assuring energy efficiency through maintenance is generally a question of keeping equipment at peak condition, especially rotating equipment and heat-transfer operations. While turnarounds and shutdowns are periods of intense maintenance activity, there is often the chance to schedule important cleaning activities even while the plants are in production. Then the question becomes when is the right time to perform the cleaning operation.
One method that has been very effective for many installations is real-time monitoring of the performance of critical heat exchangers in fouling services in order to identify when cleaning is cost-effective.
Changing stream properties and flow rates can make it difficult to know the underlying performance of exchangers, however, such that on-line correction back to a fixed base case is required. One such trend from an operating process is shown in Figure 2 below.
Tracking the overall heat transfer coefficient U can mask changes. Consider the operating periods marked in the figure.
Relatively sharp changes in the observed U value did not indicate rapid fouling, a conclusion that can be noted by comparing the changes during the same period of the U_expected value, which compensates for the process changes, and the calculated fouling factor, which displays the ultimate performance of the exchanger on the right-hand y-axis.
Figure 2: Real-time heat exchanger fouling trend compensated for flow conditions
Tracking the underlying condition in detail allowed for the cleaning operations to be scheduled at the right times, as evidenced by the sharp drops in fouling factor at the beginning and again at the end of the time period shown.
Energy management through automation
One of the simplest ways to address energy efficiency through automation is to routinely review the performance of regulatory control loops that affect energy consumption. Often these loops are not flagged by operations for attention from process control staff as long as the loop performance does not affect the production rate or final quality. By identifying and intentionally focusing on these loops periodically, it is often possible to improve energy efficiency without affecting the overall process.
Examples are steam/oil ratio controls in oil-fired furnaces, steam pressure controls for sub-headers or individual heat exchangers, plant air header pressure controls, etc. Routinely checking for poor controller tuning, valve stiction, and transmitter problems can yield benefits for many plants.
Another activity that can achieve lasting benefits is to review the control structure for ways to reduce energy consumption while meeting all processing objectives. One example that has been implemented in many sites is to set distillation column reflux flow rates to be a ratio of the feed flow rate instead of leaving the flow at a constant value.
Some columns can have a similar control strategy for the reboiler duty, varying the heat input with the column throughput. Given the objective and resources, operations and process control staff can work together to identify such opportunities in most sites.
Energy management in operations
Just as process operators are tasked with running their units safely, meeting production targets for throughput and quality, they can also address and impact energy efficiency. While a necessary first step is to measure and report energy consumption in detail and in real time, it is not sufficient in many cases.
When throughput rates, feed properties, or product qualities are highly variable, knowing how much energy should be consumed is critical additional information required. This means that operations must be given energy consumption targets that account for current process conditions so that they can spot opportunities to improve.
The importance of this point is illustrated in Figures 3 and 4 below. The steam consumption and charge rate for an operating refinery’s FCC unit are tracked in Figure 3, where several events of interest are highlighted. In the first, the steam consumption increased for a short time with no change in unit throughput. In the second event, the steam consumption increased with feed rate, as would be expected.
Figure 3: Steam consumption and feed rate for an FCC unit.
When the intelligent targeting information for the unit is added in Figure 4, the picture becomes clearer. The steam consumption targets are shown in blue; for this unit the targets depend on throughput, feed quality, and reaction conversion levels.
The excursion in steam consumption during the first event is actually worse than indicated at first since the target energy actually decreased during the event (due to process changes other than the throughput).
In the second event, although the steam consumption is expected to increase with feed rate, the increase was not executed carefully, such that the steam consumption increased more than it should have. The situation was corrected shortly after the feed rate change, such that the actual consumption was again brought in line with the target rate.
Real-time monitoring and reporting of energy consumption will allow operating staff to make moves that result in energy conservation only if the following conditions are met:
- The energy consumption must be tracked in detail – each energy/utility type, down to at least the process unit level
- The information must be tracked and reported in real time so that responses can be made as soon as a change in performance occurs
- The energy must be put into context by comparing actual consumption to a target consumption that accounts for process conditions such as throughput, feed and product quality, conversion levels, etc.
Figure 4: The same steam and feed data, now with intelligent targeting included for context.
Each person and function can impact energy efficiency
For the process industries, just as each person and job function has a part to play in ensuring production targets are achieved safely, everyone has a similar opportunity to impact energy efficiency – and most people are anxious to play their part.
When each person understands their role, are given the objectives and instructions on how to achieve them, along with the required time and resources, significant and lasting improvements can be expected. A comprehensive energy management program will address efficiency in all stages of the plant’s lifecycle, and for each role.
Rob Brendal, Asia-Pacific Manager, Honeywell